Computer-aided design (CAD) as with most design processes can be applied in different ways. The two popular CAD techniques are the: parametric and nonparametric CAD modelling techniques. These approaches to modelling have continued to generate questions among CAD users and in this post, a holistic approach to defining their differences will be taken.
What is Parametric CAD Modelling?
The use of computer programmers to design 2D and 3D models was introduced in the ‘80s and with it came parametric modelling. Parametric modelling involves the building or design of 3D geometrical models piece by piece. The process usually starts with a 2D sketch followed by the integration of constraints, dimensions, and entities to form a defined 3D model.
These constraints, dimensions, and other entities are known as parameters. Therefore, modelling techniques that make use of parameters are known as parametric modelling. Many of the CAD applications currently in circulation today, employ the parametric approach to 3D modelling.
What is Non-parametric Modelling?
Nonparametric modelling involves a direct approach to building 3D models without having to work with provided parameters. Therefore, you will not be required to start with a 2D draft and produce a 3D model by adding different entities. This means you directly model your ideas without working with pre-set constraints. That is also why nonparametric modelling is also known as direct modelling.
Today, it is a bit difficult to find CAD applications that are solely nonparametric. This is because most CAD producers integrate features of parametric modelling with features of nonparametric models. Examples of this are Rhino, Creo, and Fusion 360. These juxtaposition of features is known as synchronous modelling or synchronous technology.
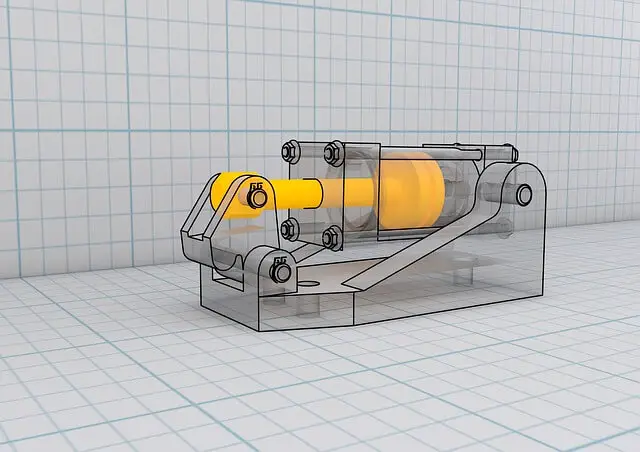
Comparing and Contrasting Between Parametric and Nonparametric Modelling
To adequately compare both modelling options, a couple of criteria will be used. These criteria include: ease of use, ability to edit, and modelling abilities. Starting with ease of use, parametric modelling works within defined parameters. This makes it easy to use when you already have the required constraints to work with. Therefore, you simply have to plan ahead and plug the constraints you have to build the 3D model.
Nonparametric modelling is different. It does not require any rigorous application of constraints or parameters. It basically allows you to manipulate the faces of a model according to what your design requires. This makes it easy to design prototypes for industrial use. Therefore, when it comes to designing truly organic, concepts, the nonparametric modelling technique is favoured by CAD users.
Moving to edits, parametric models keep ‘histories’ which define the different components in a model. This means that if you modelled a machine, each component in the machine has its own history or timeline. And if the need to edit your model comes up, you can easily select a component of the machine and edit its geometry. This process will not alter any other components of the machine. But there is a catch. Another CAD user must understand the history of the design when editing. If not, everything could come crashing down.
For nonparametric modelling, edits can be done with ease. This is due to the elimination of histories that may affect the entire design structure if changed. Therefore, CAD users can execute edits without fear of disrupting the entire machine. But some hurdles must also be surmounted. The lack of specified dimensions affects the editing process. Therefore executing edits may not produce predictable results and could lead to imbalance.
Summary
It is easy to see that both parametric and nonparametric modelling have their fair share of pros, as well as, cons. Therefore, the answer to which 3D modelling technique to use is; it depends on application. If you intend to design 3D models to be used in a defined space, parametric modelling is your best bet. Also, if these models will be used within your firm, then the limitations of understanding history while editing is eliminated.
Nonparametric modelling is best for projects where you need to ‘eyeball’ the design process. Therefore, it is recommended for prototyping design concepts. The final product of a nonparametric design process is a dumb 3D model. This makes editing easy because you do not need to dig deep into the history of each component when editing. Therefore, if you intend to share 3D models with a third-party, nonparametric modelling is the better option. To simplify the discussion on application, here is a helpful table to follow:
3D Modelling Application | Modelling Technique to Use |
Architecture | Parametric modelling |
Machine Tooling | Parametric Modelling |
Prototyping | Nonparametric modelling |
3D printing | Parametric Modelling |
Industrial Design | Nonparametric modelling |
Concept Design | Nonparametric modelling |
Synchronous Modelling Technology
In order to take advantage of the benefits of both parametric and nonparametric CAD modeling offers, the synchronous technology was introduced. As stated earlier, this process integrates features from both modeling techniques into a single CAD platform. In software applications that make use of synchronous technology, you can choose to start with a 2D sketch or a nonparametric model. This is because these applications have both parametric and nonparametric tools for your use.
Therefore, with synchronous technology, you can execute edits using histories to make dimensioning uniform. You can also choose to make quick edits by moving the face of your model. Most mainstream CAD applications and even Free 3D modeling software now make use of synchronous technology as it further simplifies CAD design. An example of this is the Fusion 360 by AutoCAD. Fusion 360 allows you to work in either nonparametric or parametric modes. Solid Edge, on the other hand, is truly synchronous and allows you to make use of both techniques simultaneously.
Conclusion
As CAD modelling continues to evolve, it should come as no surprise if every CAD tool makes use of synchronous modelling techniques in one form or the other. This is because both options have a lot to offer depending on the application. It is also important to note that the expertise of the CAD user plays a more important role in determining the quality of models and not the modelling technique used.